Relay contact rivets are generally made with a composite construction comprising a layer of the contact material bonded to an underlying copper rivet. As in everything, there are exceptions and occasionally solid contact rivets are encountered. These cost more so are only used in special cases. The quality of the rivet and its performance is influenced by the quality of the join between the two materials as well as the quality of the contact surface material itself. This can be especially important with high currents and when operating at the extremes of temperature range.
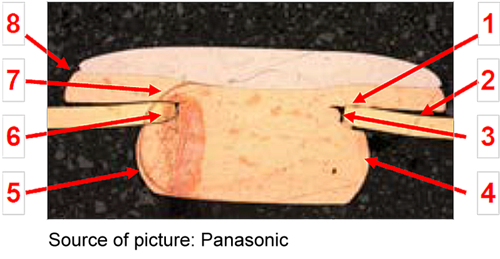
The photograph shows a poor quality rivet with many problems.
- Punching burr
- Air Gap
- Crack
- Twisted contact blade
- Rivet badly formed
- Surface pressure
- Poor hardness control in rivet
- Surface of rivet separating from copper body
Common Contact materials in Durakool Relays |
Contact Material |
Common Name |
Features |
Guide Range |
Applications |
Type |
AgNi 0.15 |
Fine Silver or Fine Grain Silver |
Silver with 0.15% Nickel. Universal but welds easily. Sensitive to atmospheric sulphur so is often available with Au flashing. (see below) |
1V to 150V
50mA to 100A
>1W
|
Resistive loads and loads switched not under power. General purpose use. |
Melt |
AgNi 90/10 |
Silver Nickel |
Silver with 10% Nickel. Important general purpose material with reduced susceptibility to welding. Good general purpose replacement for AgCdO. |
approx. 6V to 380V
10mA to 100A
|
Excellent for resistive loads with some inductive capability. A good “all rounder”. |
Sintered |
AgCdO |
Silver Cadmium Oxide |
Now banned under RoHS. Excellent general purpose power switching material. |
12V to 380V
>0.5A
>10W
|
Motor loads, general purpose power switching. |
AgSnO2 |
Silver Tin Oxide |
Excellent resistance to welding. Very good AC & DC performance. Good replacement for AgCdO in power switching. More expensive than AgNi 90/10. |
>12V to >380V
>0.5A
>10W
|
Good for motor, lamp and capacitive loads. Good general purpose use. |
AgSnOInO |
Silver Tin Indium Oxide |
More advanced version of AgSnO2 Excellent general purpose power switching. Highly resistant to welding. Good DC performance. |
>12V to >380V
>0.5A
>10W
|
Excellent for DC motor loads. Good for lamp and capacitive loads. Good general purpose material in automotive applications. |
W or AgW |
Tungsten (Wolfram) |
High resistance. Very low susceptibility to welding. Not usually used on its own. |
>60V
>1A
>50W
|
Used as a pre leading contact in conjunction with another contact (usually AgSnO2). Excellent for high inrush loads. |
|
Two common contact surface finishes are available from Durakool:
- Au (gold) plating. Typically a gold layer >2um, and may be as much as 10um (unusually) thick. The gold acts a switching surface and is very good at switching low level signals with repeatability. Will be damaged if exposed to arcs and is not recommended for switching non-resistive loads and not for high currents. Care is needed with the gold plating process to ensure an even and consistent plating.
- Au (gold) Flash. Flash is defined as a very thin (<0.3um) layer of gold plating. The purpose of which is to protect the contact rivet from atmospheric contamination or tarnishing whilst in storage. It serves little real function in normal use being eroded away as soon as the contacts start switching. Even if there is no arc, the mechanical action of the contacts wiping over each other will remove it quickly. The underlying contact material takes over to switch the load. Can sometimes be used to solve problems with automated test equipment (ATE) that only inject very small currents when testing PCB’s. After tests are complete the gold has been worn away but the gold helped the ATE to identify the contacts were closed.
Download pdf